In den letzten Jahren sind die Kosten von Photovoltaik stark gefallen. Heute sind die Stromgestehungskosten von Solarmodulen bereits so niedrig, dass sie mit denen von fossilen Energieträgern konkurrieren können. Dies wurde durch die Integration von F&E Ergebnissen, aber auch durch den schnellen Ausbau an Produktionskapazitäten für die Silicium Photovoltaik erreicht. Durch die Fokussierung auf die Kostenreduktion stand der Aspekt der Nachhaltigkeit bisher nicht so sehr im Vordergrund. So gibt es unter anderem noch Verbesserungspotenzial beim Energie- und Rohstoffverbrauch während der Herstellung. Forschungsarbeiten, die zukünftig eine möglichst ressourcenschonende, lokal produzierbare Photovoltaik ermöglichen, sind daher wünschenswert. Am Fraunhofer ISE wurde aus dieser Motivation heraus das Konzept der »in-situ« Herstellung von gedruckten Solarmodulen erfunden und weiterentwickelt.
»Einsparung durch Integration«
Bei der Entwicklung und der Beurteilung des Potenzials von neuen Photovoltaiktechnologien steht zuerst die Erforschung des photoaktiven Materials im Vordergrund. Dazu werden oft in der Herstellung zunächst aufwändige Laborzellen entwickelt. In einer späteren Produktion ist man dann damit konfrontiert, viele unterschiedliche Prozessschritte optimieren und in den Produktionsfluss integrieren zu müssen. Wenn kein geeignetes Produktionskonzept besteht, kann dies die Markteinführung erheblich erschweren. Um das zu vermeiden, muss bei der Entwicklung möglichst frühzeitig auch die Produktionstechnologie bis hin zum Modul betrachtet werden. Als interessantes Konzept in diese Richtung erforscht eine Arbeitsgruppe am Fraunhofer ISE „in-situ“ Solarzellen, bei denen Materialentwicklung und Modulentwicklung von Anfang an integrierbar sind. Hierbei wird der bisher bekannte Herstellungsablauf eines PV-Moduls – von der Zelle zum Modul – so umgekehrt, dass zuerst das Solarmodul gefertigt wird und anschließend das eigentliche photovoltaische Material eingefüllt wird, um dann im Inneren des Moduls »in-situ« – aktiviert zu werden. Als besonders geeignetes photovoltaisches Material hierfür werden Perowskite untersucht.
Lokale Produktion und Vertrieb
Wenn es gelingt, sehr preisgünstige Absorbermaterialien mit einfachen Herstellungsverfahren zu kombinieren, dann reduzieren sich die Materialkosten von Solarmodulen nahezu auf die Kosten der Glassubstrate. Eine Herstellung über dezentrale Wege mit lokalen Produktionsstätten wäre dann nicht nur an hochtechnisierten Standorten, sondern auch unter einfacheren Infrastrukturbedingungen realisierbar. Für die spätere Vermarktung von gedruckten »in-situ« Solarzellen könnte idealerweise also das Geschäftsmodell der glasproduzierenden und verarbeitenden Industrie übernommen werden. Dies bedeutet, dass aufgrund der niedrigen Materialkosten die Transportkosten anteilmäßig den Verkaufspreis so erhöhen, dass lokale Produktion und Vertrieb gegenüber einer zentralisierten Herstellung global gesehen konkurrenzfähiger werden.
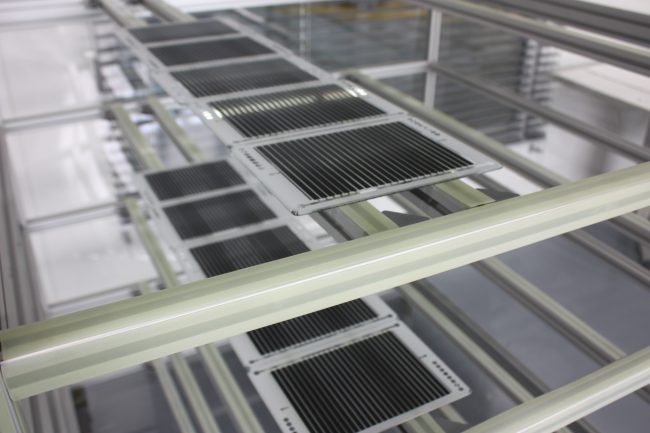
CO2-Bilanz der Herstellung von Solarmodulen optimieren
Trotz des starken Wachstums der Produktion liegt der Anteil von Photovoltaik an der Stromversorgung weltweit erst bei etwa einem Prozent. Für den weiteren Zuwachs spielt auch der in der Modulproduktion anfallende Rohstoff- und Energieverbrauch eine zunehmende Rolle. Eine wichtige Kenngröße zum Vergleich mit anderen Energietechnologien ist der sogenannte CO2 Fußabdruck gemessen in Gramm CO2 pro Kilowattstunde erzeugter elektrischer Energie. Hier gilt, je geringer der Energieaufwand für die Herstellung ist und je höher die erzeugte solare Leistung ist, umso besser für die Bilanz. In einer ersten Abschätzung läge dieser Wert für in-situ Solarmodule bei sehr niedrigen 15 g / kWhel. Hierbei wurde ein Betrieb der Module über 20 Jahre in Südeuropa angenommen. Der Wert für ein Braunkohlekraftwerk liegt bei etwa 1 kg / kWhel.
In-situ Konzept: Integration von Solarzellen- und Modulherstellung
In unserem bereits 2013 patentierten Konzept der in-situ Solarzellen wird die Reihenfolge der Prozessschritte für die Herstellung des Solarmoduls umgekehrt, sodass das photovoltaisch aktive Material als letzter Schritt eingebracht werden kann. Dafür werden als Ausgangspunkt auf einem leitfähigen Glassubstrat bereits in Modulgröße Schicht für Schicht poröse Elektroden-Strukturen mittels Siebdruck aufgebracht. Diese als Grundgerüst dienenden Elektroden werden dann mit einem zweiten Glassubstrat versiegelt. Das Modul ist damit bereits fast komplett fertig. Anschließend wird im letzten Prozessschritt ein verflüssigtes photoaktives Absorbermaterial eingefüllt, welches wie von einem Schwamm von den porösen Strukturen der Elektroden aufgesaugt wird und sich im Modul verteilt. Hier findet dann die Kristallisation des Absorbers statt.
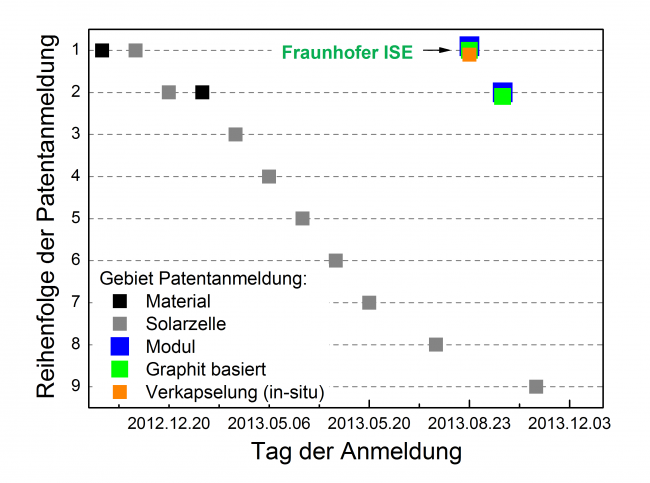
Als Absorbermaterial für das in-situ Konzept eignen sich neuartige Perowskite besonders gut. Ein besonderes Kennzeichen dieser Art von Perowskiten ist, dass für Solarzellen mit Schichtdicken von weniger als einem Mikrometer verblüffend hohe Wirkungsgrade erzielbar sind. Demensprechend groß ist seit 2013 das Interesse in der Forschungsgemeinschaft. Hier ist es uns gelungen, die Patentanmeldung zu in-situ produzierbaren Solarmodulen als skalierbares Konzept für Perowskit basierte Photovoltaik zu platzieren Für eine realistische Skalierung ist das in-situ Konzept besonders gut geeignet, da aufgrund der Glaslotversiegelung zwischen den spannungsmäßig verschalteten Zellen eines Solarmodules eine Ionendrift verhindert werden kann. Für Perowskit als ionisches Material mit Salzcharakter ist eine schädliche Ionendrift sonst unvermeidbar. Eine direkte Adaption von bestehender Dünnschichttechnik, bei der keine ausreichende Barriere zwischen Zellen besteht, ist somit für langzeitstabile Perowskitsolarmodule nicht möglich.
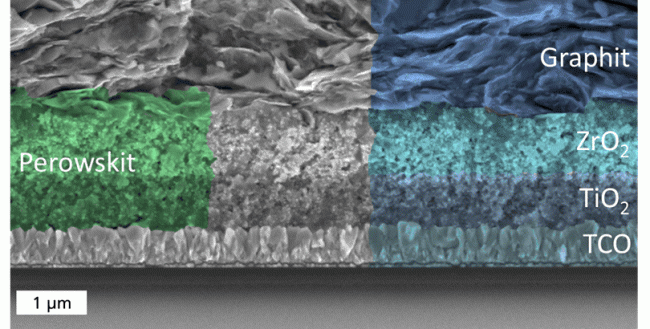
Fällt Licht auf den absorbierenden Perowskit, so entstehen positive und negative elektrische Ladungsträger. Diese Ladungen müssen aus der Solarzelle heraustransportiert werden, damit elektrische Energie gewonnen werden kann. Poröses Titandioxid dient hierbei zur Extraktion der negativen Teilchen. Die zurückbleibenden positiven Ladungen werden vom Titandioxid abgewiesen und auf der anderen Seite der Zelle, getrennt durch eine Isolatorschicht, über eine Schicht aus porösem Graphit abtransportiert. Die Elektrodenmaterialien sind sehr günstig, langlebig und lassen sich einfach drucken. Für den Perowskitabsorber müssen aufgrund der Schichtdicke von unter einem Mikrometer nur geringe Mengen verwendet werden. Die Komponenten des Salzes lassen sich einfach aus im großen Maßstab vorhandenen Grundchemikalien synthetisieren.
Kristallisation aus einem geschmolzenen Perowskitsalz
Eine große Herausforderung bei der Herstellung solcher Zellen stellte bislang das gleichmäßige Befüllen und Kristallisieren des Perowskits in den porösen Strukturen dar. Zur Verflüssigung wurde bisher der Perowskit in einem Lösungsmittel aufgelöst. Dieses Lösungsmittel muss jedoch wieder entfernt werden, um den Perowskit zu kristallisieren. Dafür wird die befüllte Zelle erhitzt, sodass das Lösungsmittel verdampft. Bei diesem Schritt kommt es zu unkontrollierten Bewegungen in der Flüssigkeit und zurück bleiben unregelmäßig getrocknete Strukturen. Dabei laufen beim Trocknen aus Lösungsmitteln ähnliche Prozesse ab, wie sie auch bei dem sogenannten Kaffeering-Effekt bekannt sind, um zu erklären warum der Rand dunkler als die Mitte ist.

Das Problem mit der ungleichmäßigen Trocknung des Lösungsmittels in in-situ Zellen konnten wir nun mit einem neuen, 2018 zum Patent angemeldeten, Ansatz umgehen. Hierbei wird zuerst der Perowskit als pulverförmiges Ausgangsmaterial mit einem polaren Gas überströmt. Dadurch verändert sich das Perowskitsalz so, dass es bei Raumtemperatur reversibel aufschmilzt und nun in flüssiger Form vorliegt. Diese Schmelze kann dann in die porösen Elektrodenstrukturen eingebracht werden. Durch Desorption, also Austreiben des polaren Gases, steigt der Schmelzpunkt des Perowkits wieder stark an und der Absorber kristallisiert wie gewünscht in den Poren. Hierdurch kann eine sehr homogene Verteilung des Perowskits im Modul erreicht werden. Weniger als zwei Milliliter des geschmolzenen Salzes werden für die Herstellung von einem Quadratmeter benötigt.
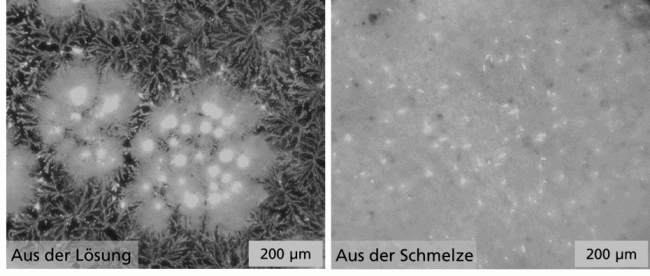
Zertifizierter Rekordwirkungsgrad für gedruckte Perowskit-Solarzellen
Der Wirkungsgrad für die Umwandlung von Sonnenlicht in elektrische Leistung gilt als das wichtigste Merkmal einer Solarzelle. Bei etablierten Technologien wie Silicium-Photovoltaik wird dafür unter einer normierten Beleuchtungsquelle, die das Sonnenlicht simuliert, eine Kennline des Zellstroms für verschiedene angelegte Spannungen in kurzer Zeit aufgezeichnet und daraus der Wirkungsgrad bestimmt.
Bei der jungen Technologie Perowskitsolarzellen weist sich die bisherige Herangehensweise der Wirkungsgradmessung jedoch als schwierig. Perowskit, als photovoltaisch aktives Salz, besitzt nämlich ein „Gedächtnis“ für vergangene Messbedingungen. So kann eine zuvor angelegte Spannung oder Beleuchtung das Ergebnis der Strom-Spannungs- Kennlinie stark beeinflussen. Der tatsächliche Wirkungsgrad einer solchen Solarzelle auf einem Hausdach oder einer Gebäudefassade kann auf diesem Weg nicht genau bestimmt werden.
Wie wir kürzlich zeigen konnten, besteht ein verlässlicherer Weg zur Bestimmung des Wirkungsgrads von Perowskitsolarzellen darin, die Zelle bei konstanter Beleuchtung und konstanter angelegter Lastspannung über längere Zeiträume zu vermessen – wie dies auch später unter realen Bedingungen Fall ist. Dabei wird die »Erinnerung« der Zelle an vorherige nicht-stationäre Zustände gelöscht.
Mit dieser Messmethode wurde für unsere mit dem geschmolzenen Salz hergestellte gedruckte Perowskitsolarzellen ein stationärer Wirkungsgrad von 12,6 % auf 0.1 cm2 und eine Photospannung von 1.0 V vom Fraunhofer ISE CalLab PV Cells zertifiziert. Dies ist nebenbei bemerkt auch der höchste derart zertifizierte Wirkungsgrad für gedruckte Photovoltaik im Allgemeinen. Über die wissenschaftlichen Hintergründe dieser Arbeiten berichteten wir in den renommierten Zeitschriften Nature Scientific Reports und ACS Energy Letters.
Das Fraunhofer ISE koordiniert ein vom Bundesministerium für Bildung und Forschung BMBF gefördertes Verbundprojekt MesoPIN zur Materialentwicklung von gedruckten Perowskitsolarzellen. Projektpartner sind die Universitäten Konstanz, Bayreuth und Freiburg sowie die Firmen Opvius GmbH in Nürnberg und Kitzingen und Thieme in Teningen.
Weitergehende Untersuchungen zur industriellen Aufskalierbarkeit finden im Rahmen des Fraunhofer MAVO Projekts PeroTec statt. Kooperationspartner: Fraunhofer IWM, Fraunhofer ISC und das Fraunhofer ISE (Koordinator).
Kommentieren